Challenged to devise a way to extract and forge metal on the moon, a team of University of Utah engineering students has won top honors in a NASA-sponsored competition with their proposal for refining the iron that is abundant at the lunar surface.
The group, led by John Otero and Collin Andersen, graduate students at the U’s John and Marcia Price College of Engineering, adapted a century-old process known as carbonyl iron refining, or CIR, for use in a lunar environment with its non-existent atmosphere, freezing temperatures and low gravity. They proposed using a two-chamber process in which a reactive gas phase concentrates disparate iron particles into a powder product that is more than 98% iron with properties favorable for additive manufacturing, according to their presentation.
“There were multiple times we came close to scrapping the concept, but each time we found the strength to go a little farther. Our small group was driven by a genuine belief in the concept and curiosity of what would happen,” said Andersen , a doctoral student in materials science and engineering from Providence, Utah. “This honor has validated the perseverance, effort, and dedication of exploring an innovative and applied idea.”
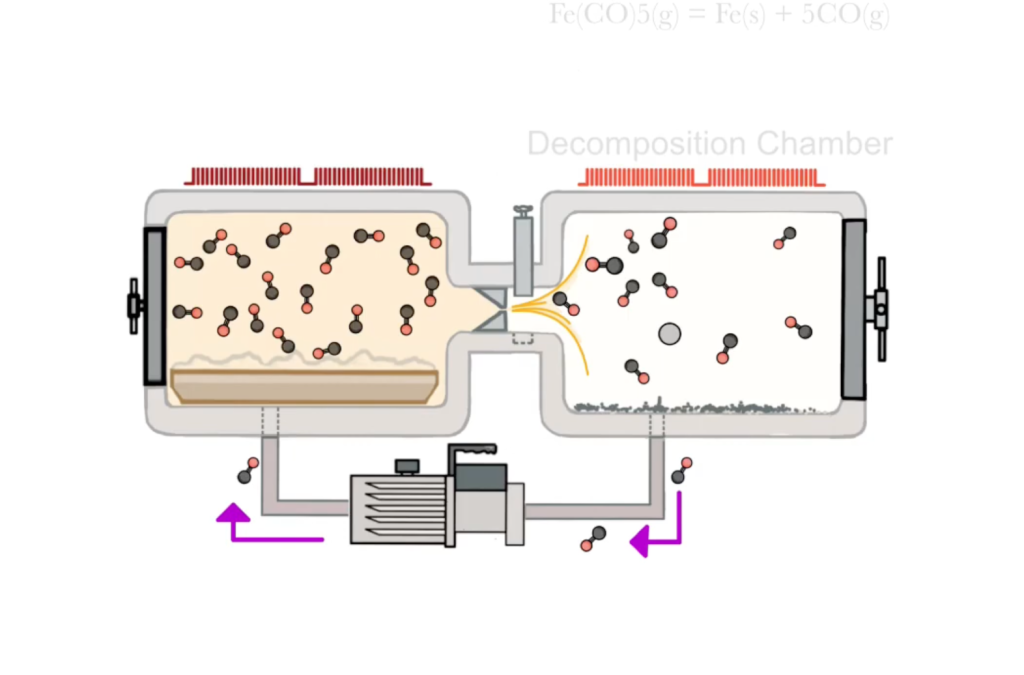
This illustration shows the two-chamber process proposed by U engineering students for refining iron on the moon.
The Utah idea took home the Artemis Award at the BIG Idea Challenge held last week in Ohio, where finalist teams representing seven universities presented their projects to a panel of judges. The aim of the competition, titled “Lunar Forge,” was to explore ways to enable the development of the lunar surface with “in-situ resource utilization” (ISRU), that is using resources available on the moon rather than transporting them from Earth.
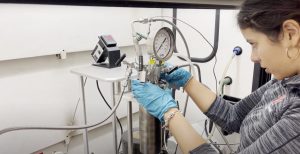
Team member Juliana Ortiz handles a pressure vessel used for refining iron. In the top photo, University of Utah engineering students, left to right, John Otero, Christian Norman, Olivia Dale and Collin Andersen celebrate their team’s win at NASA’s 2023 BIG Idea Challenge held last week in Ohio.
Contestants were instructed to “design, develop and demonstrate technologies that will enable the production of lunar infrastructure from ISRU-derived metals found on the moon.” End products included storage vessels for liquids and gases, extrusions, pipes, power cables and supporting structures, such as roads and landing pads.
Plenty of iron on the Moon, but not much carbon
Onsite and self-sufficient metal production is essential to NASA’s goal of building a sustained human presence on the lunar surface.
Nearly the entire lunar surface is covered in an unconsolidated glassy material called regolith, formed over the past 4 billion years from meteor strikes. It’s the regolith that contains iron, as well as oxygen and silicon, which may also be helpful for lunar development.
“Transporting metal to the moon is difficult and expensive. Fortunately, the moon’s surface is rich in iron, but how can we put that metal to work?” said U team co-leader John Otero in a project video. Like Otero, most of the U students involved study in the Department of Metallurgical Engineering. Others are with the Department of Materials Science & Engineering.
The group proposed harnessing the constituents of regolith to facilitate a refining process that would need little in the way of imported equipment or resources.
“In the formation chamber, high carbon monoxide partial pressure favors the formation of iron pentacarbonyl gas. The iron-bearing gas is carried into a second low-pressure chamber where the gas undergoes thermal decomposition into a metal product,” explained Andersen in the video. “The carbon monoxide is pumped back into the formation chamber for immediate reuse.”
In other words, the process is a closed loop that can feed itself, yielding a product that can be used to build lunar infrastructure. As they tested the process over the past few months, the team realized some of its aspects were well suited foe a lunar environment, according to Andersen. The first was how the precious oxygen in the carbon monoxide could be used over and over again.
“It only has to be periodically regenerated and, hang on, we realized that the way to regenerate it utilized waste material from the lunar life support system,” he explained in an interview. But there’s more
“This is probably the big kicker that really sealed the lunar advantage, and that is that CIR accomplishes three things simultaneously,” Andersen said. “The first thing it does is concentrate the iron, which is something that is rather difficult to do and takes multiple steps on Earth.”
Then it purifies the iron and renders it in a form that can be used in 3D printing.
“The iron powder exhibits excellent size and morphology characteristics for use in metal additive manufacturing,” said team member Jarom Chamberlain. “The particles can also be grown large to facilitate traditional casting. Later on, the apparatus doubles as a carburization chamber to surface hardened finished parts.”
One tool, many uses
On the Moon, every tool is expected to have several uses.
“You don’t just want to have a hammer. You want a hammer that functions to do something else, maybe three things at once, and that’s essentially what this technology is doing,” Andersen said.
The main challenge was to make the process work in the lunar environment, which is vastly different than anything on Earth. Carbonyl iron is currently produced at pressures above 200 atmospheres (or atm, a unit of air pressure typically found at sea level.)
“This is not practical for lunar deployment,” Chamberlain said. “However, with a modest reduction in formation temperature, adequate formation is predicted at 60 atmospheres or less.”
Other team members included Olivia Dale, Christian Norman, Cole Walker, Jason Sheets, Talon Townsend, Juliana Ortiz, Olivia Slane, Jordan Contreras, Jacob Burke and Cristian Urbina. Their faculty advisors were Hong Yong Sohn, Michael Simpson and Zhigang Zak Fang. Further guidance was provided by Fang’s Powder Metallurgy Research Lab.
NASA’s Breakthrough, Innovative and Game-changing (BIG) Idea Challenge is an annual nationwide competition that gives college students the opportunity to play a pivotal role in the future of space exploration. In response to a yearly prompt that tasks participants to solve a specific space-based problem, teams of undergraduate and graduate engineers get to work developing creative and innovative concepts. After all project proposals are submitted, five to eight teams are selected to receive a combined total of $1.1 million to further build and develop their system, which they present at the BIG Idea Forum in the fall of that year.
Joining Utah as this year’s finalists were the Colorado School of Mines, Massachusetts Institute of Technology, Missouri University of Science and Technology, Northwestern University, Penn State and University of North Texas.
Moon photo and video on utah.edu homepage courtesy NASA
MEDIA & PR CONTACTS
-
Evan Lerner
Director of communications, John and Marcia Price College of Engineering
801-581-5911 evan.lerner@utah.edu