The promise of flexible, reliable, emissions-free power has inspired dozens of U.S. companies and universities to design the next generation of nuclear power reactors.
Many of these advanced reactors feature safety systems that rely on the laws of physics to automatically shut down a reactor in case of an accident. Some would also reach temperatures high enough to power industrial processes such as hydrogen production, and most would work in tandem with intermittent renewables to balance power generation with loads on the electrical grid.
To make these technologies a reality, U.S. reactor developers and Congress have asked for a scientific machine to test the fuels, materials and sensors.
That machine, the U.S. Department of Energy’s proposed Versatile Test Reactor, will produce high levels of fast-neutron radiation to mimic, in weeks or months, the effects sustained over years or decades in a power reactor core.
The accelerated experimental results achieved with VTR will benefit materials development for today’s water reactors as well.
Even as the Versatile Test Reactor makes its way through the federal approval process, the VTR team has already begun collaborating with industry and academia to prepare experiments in anticipation of the VTR’s construction.
One such collaboration—among researchers from the University of Utah, the University of Michigan, and Virginia Commonwealth University — is designing experiments to test various molten salt reactor technologies.
The university researchers are working within a larger group that includes Oak Ridge National Laboratory, Idaho National Laboratory, the University of Idaho and TerraPower, a Washington-based nuclear innovation company that is leading the molten salt experiment design effort. The group is designing “experimental test vehicles” that will be inserted into the Versatile Test Reactor’s reactor core.
“There’s very little data on irradiating these salts with neutrons,” said Michael Simpson, professor of materials science and engineering at the University of Utah. “We came up with this idea to irradiate molten salt and to see how the molten salt would change.”
Experimental vehicles are essentially cartridges that contain all the necessary components—fuels, metal alloys, nonmetallic materials, sensors, coolants and other advanced components—of a given experiment.
“It’s a real design challenge,” said Joel McDuffee of Oak Ridge National Laboratory. “All these components that go into the cartridge are also affected by the neutron radiation, so we have to do a lot of testing to make sure the cartridge can last as long as the molten salt.”
VTR technicians will insert these test vehicles into one of the many test positions in VTR’s reactor core for the prescribed amount of neutron radiation, then retrieve the experiment for examination.
“One of the big advantages is you can do ultra-accelerated tests in the VTR,” said Kevan Weaver, an INL technical lead. “The way that the core and the experiments are integrated in the core design, we can perform gas-cooled, molten salt, lead and sodium experiments. There’s a ton of combinations of the types of experiments we can do.”
Simpson and his colleagues say the Versatile Test Reactor is essential to answering big science questions about how to build these power reactors so they operate safely and efficiently.
Specifically, the research team is building a test vehicle that would circulate the molten salt to mimic how it would circulate through a real-world reactor. “It’s like you’ve got a small molten salt reactor inside of the VTR,” Weaver said.
What is a molten salt reactor?
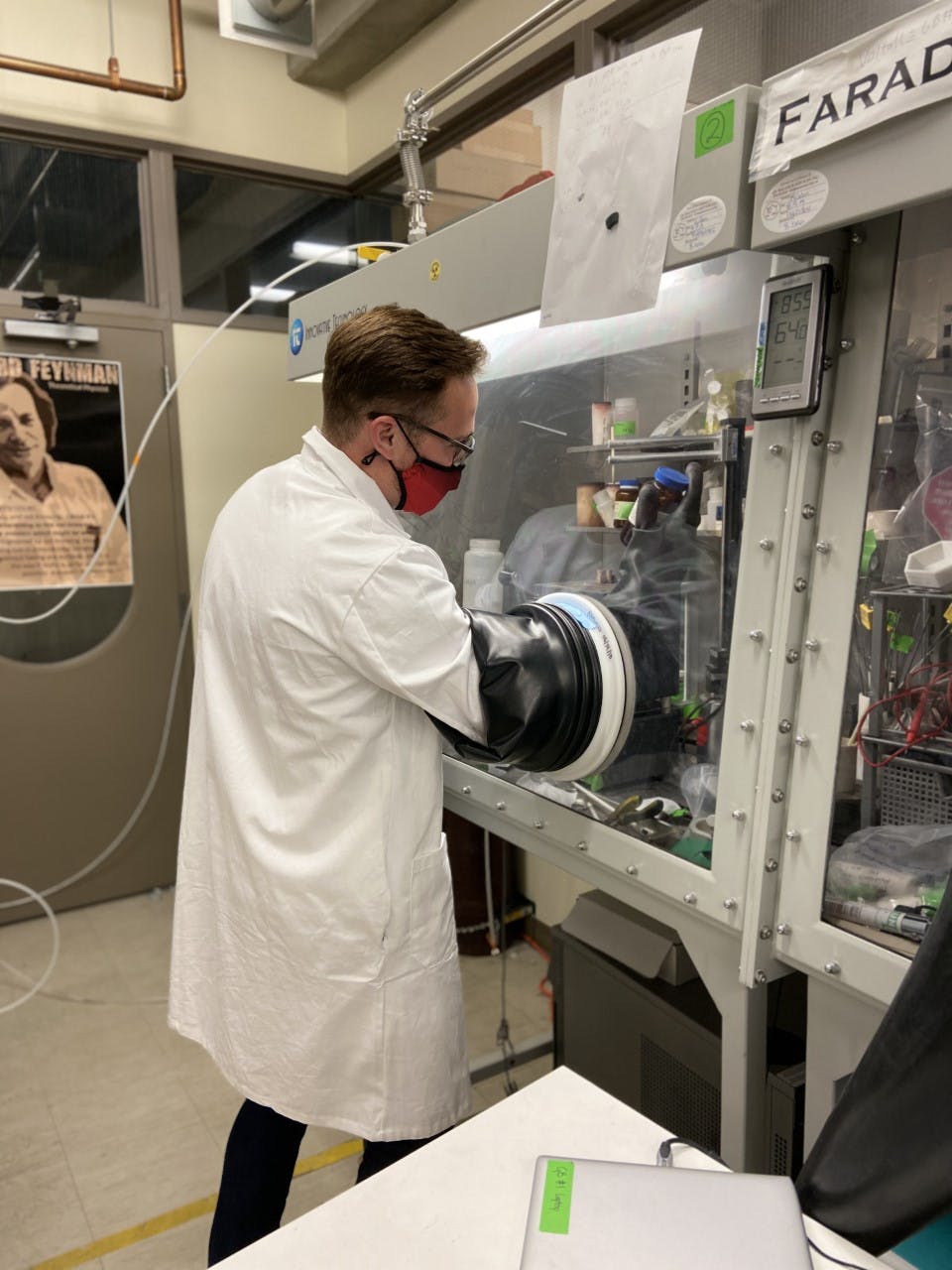
PHOTO CREDIT: Courtesy of the Simpson laboratory.
Matt Newton, a graduate student in the Simpson laboratory.
Download Full-Res ImageIn a full-size molten salt power reactor, a molten salt/fuel mixture flows through the reactor core, where it is heated via nuclear reactions before circulating through a heat exchanger.
Molten salt reactors are considered an attractive alternative because the high temperatures needed to melt the salt can be used to generate electricity with high efficiencies or as process heat for industrial applications.
The reactors themselves are also relatively simple and therefore economical to build and operate, said team member Supathorn Phongikaroon, director of nuclear engineering programs at the VCU College of Engineering.
“One of the reasons the front-end cost of conventional light water reactors is so high is because of the high pressures,” said Phongikaroon. “Molten salt reactors operate at low pressures, which means the capital investment potentially is much less.”
Molten salt reactors also are flexible enough to follow loads on the grid and are considered walk-away safe.
“If there’s an accident, the molten salt cools and becomes solid,” Phongikaroon said. “Typically, you don’t have to worry when the salt turns back into a solid.”
Another benefit of molten salt reactors is continuous refueling. There’s no need to shut down the reactor because the nuclear fuel is added to the molten salt coolant during operation.
All things considered, molten salt reactors overcome many of the limitations inherent in conventional light water reactors, said Simpson.
“Salts have the right physical properties,” he said. “A lot of those water reactor limitations go away when you’re dealing with molten salt and, at 500 to 700 degrees C, you can make electricity very efficiently.”
Managing corrosive salts, neutron radiation
If molten salt reactors have two big challenges, it’s that the salts are highly corrosive and that heavy neutron exposure could change the salt chemistry.
Understanding how those changes in chemistry affect corrosion is a key challenge for Simpson and his colleagues.
VTR will help the team develop models about how that chemistry is going to change.
“Once a uranium atom splits, the fission products can recombine with ions in the molten salt,” Simpson said. “It matters whether the fission product is a chloride or a metal or a gas. That’s going to affect the corrosivity of the salt. We need data to know how this works.”
VTR will help the team develop models about how that chemistry is going to change. “Once a uranium atom splits, the fission products can recombine with ions in the molten salt,” Simpson said. “It matters whether the fission product is a chloride or a metal or a gas. That’s going to affect the corrosivity of the salt. We need data to know how this works.”
Each member of the team—which also includes Xiaodong Sun, a professor at the University of Michigan’s nuclear engineering and radiological sciences department—is an expert in one piece of the puzzle, and VTR helps them put that puzzle together.
For example, part of Phongikaroon’s focus will be measuring transport properties of the salt such as viscosity and surface tension, while Sun handles the fluid mechanics, and Simpson handles the chemistry.
“VTR allows us to understand the interaction between nuclear physics, chemistry and nuclear engineering,” said Phongikaroon. “Corrosion happens on the chemistry level, but it also happens on a larger scale.”
Sun agreed that the challenges are complex. “In addition to the chemistry, you have fission gases you need to remove at least partially during the reactor operation,” he said. “And some of the fission products could plate out on the pipe walls. There are a lot of phenomena and physics involved.”
When complete, the Versatile Test Reactor will be the only reactor of its kind in the United States and one of a few that exists in the world. Access to those foreign reactors is limited, and protecting intellectual property is tricky.
VTR will offer researchers like Simpson, Phongikaroon and Sun more than just a facility to irradiate their samples. It also offers them the capabilities and expertise of the national laboratory system. That includes hot-cell examination facilities and help with experimental design.
“It’s been great working with INL to bring industry together with the universities and national labs,” Simpson said. “We hope we can keep the momentum going.”
Find the original post on the Idaho National Laboratory website.